Efficient and Sustainable Adherent Cell Cultivation with CellScrew
Challenges of Conventional Adherent Cell Culture Systems
Single-use, disposable containers made of petroleum-based plastics, such as T-flasks or multi-tray vessels, are the dominant systems used for adherent cell culture practices. However, the limited oxygen and nutrient exchange in these systems, the labor-intensive practices involving frequent media exchange, and the large carbon emissions during manufacture of fossil-fuel based plastic products are major disadvantages of the current systems. Depending on the cell culture and production scale, many heavy, bulky vessels are used. These existing systems reduce efficiency in laboratory practice and take up large amounts of valuable lab space, inevitably slowing down development and production of innovative therapies.
Increasing Production Efficiency
The Green Elephant CellScrew™ Cell Culture System simultaneously addresses process efficiency challenges and the environmental burden associated with existing adherent cell culture systems, all while prioritizing cell cultivation conditions.
"The novel cell culture vessel combines innovative structures and plant-based plastic to help simplify cell culture processes and increase environmental sustainability."
The internal geometry consisting of concentric cylinders offers an exceptionally large growth surface for adherent cells – the CellScrew™ 10K offers a growth surface of 10,000cm2 and weighs only about 850g, meaning one CellScrew™ 10K can replace 133 T-75 flasks or 12 roller flasks. Furthermore, the CellScrew™ is a compact and easy-to-handle system, reducing manual labor and improving production efficiency.
Ideal Cultivation Conditions for Adherent Cells
The predominant adherent cell culture vessels in use are static systems that limit consistent gas and nutrient exchange. Alternative methods employing rockers or shakers pose the risk of subjecting cells to high shear forces. The CellScrew™ integrates Archimedes’ screws to transport medium throughout the bottle when rotated on a roller bottle device, allowing for excellent mixing of the medium and thorough gas exchange while maintaining low shear forces. As an added benefit, experiments have shown that trypsin concentration can be reduced by approximately 66 percent while maintaining harvesting efficiency.
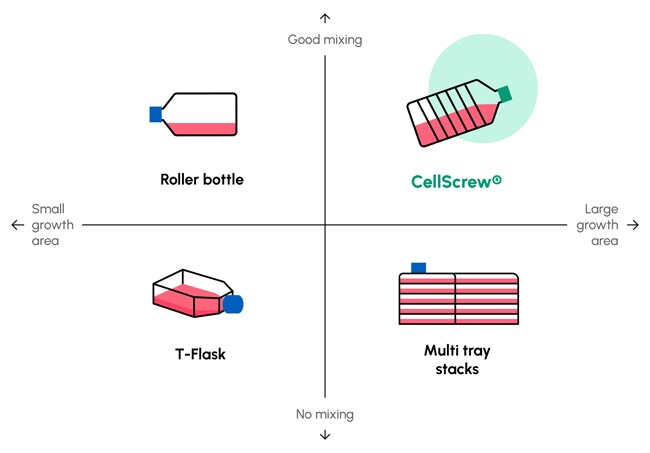
An Environmental Advantage
The CellScrew™ is produced using additive manufacturing, which allows for the intricate internal structure. As a result, less material is required to achieve a large growth surface than in conventional cell culture vessels. It is made of environmentally-friendly polylactic acid (PLA), a bioplastic derived from the fermentation of plant starch. CellScrew™ releases only the amount of CO2 that was previously bound in the corn or sugar cane plant, the raw material of PLA. Overall, these advantages mean the product can reduce CO2 emissions by up to 90 percent compared to conventional petroleum-based cell culture vessels providing the same growth area. Apart from its low CO2 emissions, the biopolymer exhibits additional benefits such as being non-toxic and biocompatible. It is well-tested and widely utilized in medical technology, including implants and scaffolds for regenerative medicine. These properties, along with its ability to be easily surface-treated for cell growth and adhesion, make the material suitable for cell culture. Experiments on the PLA surface have shown improved growth and attachment compared to polystyrene surfaces for various adherent cell lines.
Simplifying Scale-Up
A further challenge in biopharmaceutical manufacturing is often scale-up: How can processes that prove successful in the lab be efficiently transferred to the production scale? All of these processes must be carefully controlled, documented, and adhered to. This is where CellScrew™ offers a decisive advantage: It is applicable at all stages of development and, when transitioning from laboratory to production scale, the CellScrew™ processes require only minor adjustments, while the growth conditions for the cells remain highly similar.
Summary
Moving towards more sustainable, efficient laboratory practices will transform both development and manufacturing, and increase access to and affordability of scientific innovations, all while reducing the life science industry's carbon footprint.
Content provided by: